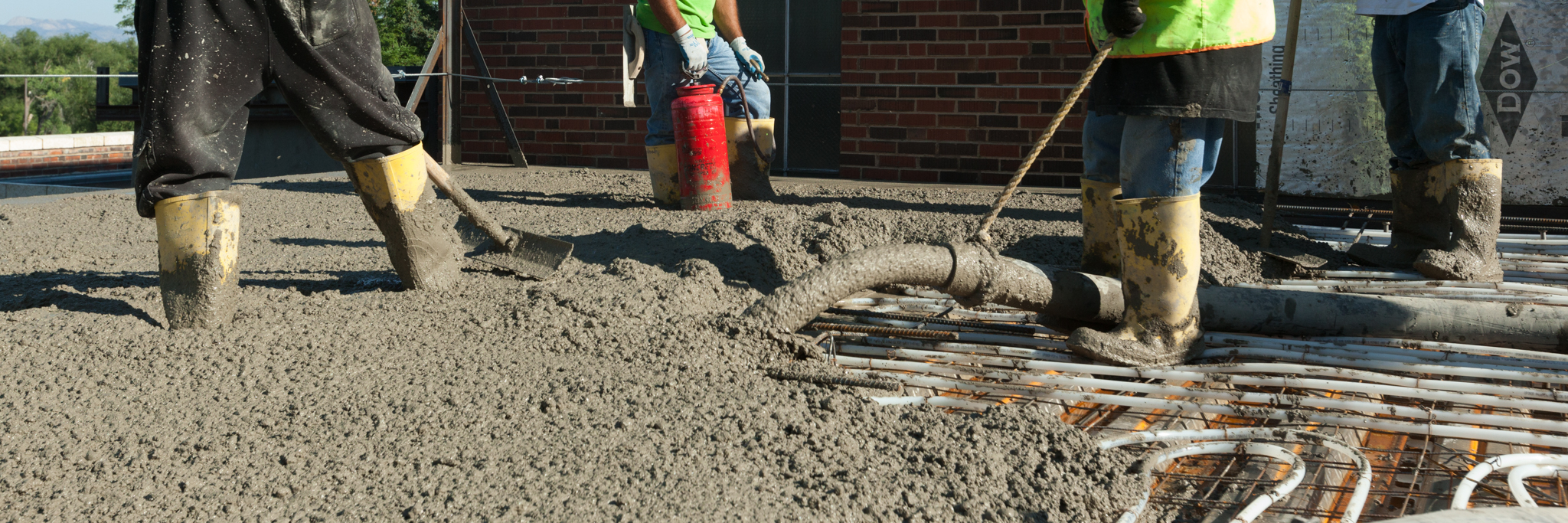
Home
Mass Timber Rising
Sustainable Forests
Tall Wood – Low Carbon
Fuels to Frame
About
The Greening of the Grid
A Future Built of Wood
Why Upfront Carbon Matters
A greener grid shifts the spotlight from operational emissions to construction emissions. These emissions, often called upfront carbon, include emissions from raw material extraction, processing, transporting, and the actual onsite construction. Conventional materials can account for close to 90% of those emissions in medium-rise (8- to 18-story) buildings, but by designing with mass timber, these upfront emissions can be reduced up to 44%. And those reductions can be made today, when they matter most.
The conceptual animation illustrates how the relative importance of upfront carbon (emissions released before the building is completed) increases as the carbon intensity of the energy needed to operate a building decreases. (Based on United Nations Environment Programme’s 2020 Global Status Report and grid decarbonization targets of Oregon and Washington.)
For a new medium-rise office building (8 to 18 stories), around 90% of upfront emissions are due to the production of concrete (~75%) and steel (~15%).1
Emissions from upfront carbon are particularly important today because they immediately add CO2 to the atmosphere which remains there between 300 and 1,000 years.
Although the concrete and steel industries are beginning to reduce their emissions, it is a slow and challenging process. All of the upfront fossil emissions are released into the atmosphere before the building is occupied. And those emissions remain in the environment well beyond the life of the building.
Mass timber changes the equation
Fortunately, a lower carbon material is available today. A mass timber medium-rise office building in the Pacific Northwest is estimated to have 30% to 44% less upfront carbon than a conventional concrete and steel design.
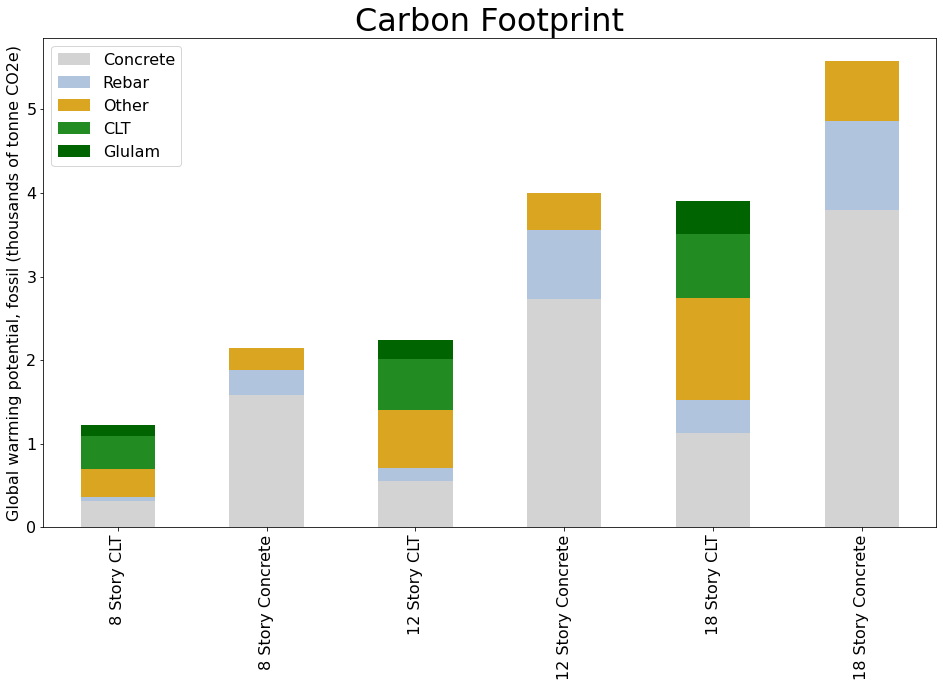
The data shown here is based on active research that directly compares the life cycle impacts of functionally equivalent mass timber and conventional concrete building designs. The study created detailed designs of a pair of three different size (8-, 12-, and 18-story) mix-use buildings using the AutoDesk Revit building information modeling (BIM) tool. A cradle-to-gate (A1-A5) LCA was conducted on all six designs with SimaPro software tool using Ecoinvent, Datasmart, and CORRIM databases.3
End-of-life and stored carbon in the building materials
What happens to the wood at the end of a building’s life is important. However, it is likely that when a building is ready for deconstruction, future policies, markets and technology will find a better use for that carbon.
Most estimates assume that at the end of a building’s life (often assumed to be 90 years for a well-designed and constructed office building) all of the stored carbon will be released back to the atmosphere. However, reuse, down-cycling, and even deep burial can keep that carbon out of the atmosphere for much longer — even centuries.
Why steel and concrete are challenging to decarbonize
The two most common building materials for commercial buildings are concrete and steel. Both are very energy intensive and significant emitters of greenhouse gases — together totaling nearly 14% of global greenhouse gas emissions.
Not only do those emissions come from burning fossil fuels for heat and electricity, but a significant amount of the emissions come from the fundamental chemistry of producing these materials. Reducing the carbon footprint of these materials is complex and challenging.
Deeper Dive: Ore to Iron and Steel
The iron and steel sector are responsible for more than 7% of global GHG emissions — mostly from the direct and indirect use of fossil fuels for heat, electricity, and processing. Steel is a metal alloy of iron (around 99%) and carbon (around 1%). Stainless steel alloys have an additional 10%+ of chromium.
Virtually all the naturally occurring iron in the crust of the earth is in the form of iron oxide (primarily and
) — basically rust. Processing iron ore into iron metal is one of the most energy and carbon intensive parts of the iron and steel making process. And it is one of the most challenging to decarbonize.
Commercially, the oxygen in the ore is removed by using coal (essentially pure carbon) to first produce carbon-monoxide (), and then reacting it with iron oxide to produce metal iron and
. The carbon-dioxide is released into the atmosphere.
Step 1:
Carbon + Oxygen → Carbon-monoxide
Step 2:
Carbon-monoxide + Iron-ore → Iron + Carbon-dioxide
Since virtually all the carbon is fossil coal, the is also a GHG. However, biogenic carbon in the form of charcoal can be used. This is how iron was historically produced, including iron smelted in Lake Oswego, Oregon in the second half of the 1800’s. If the charcoal is sustainably produced, the resulting
is considered biogenic.
Today, one of the most promising non-fossil carbon approaches is to use hydrogen gas produced by splitting water with electricity generated from non-carbon energy sources (hydro, wind, solar, and nuclear).
Step 1:
Water + Energy → Hydrogen + Oxygen
Step 2:
Hydrogen + Iron-ore → Iron + Water
Only steam is released into the atmosphere.
This is now being tested at pre-commercial scale, but transforming the whole industry will likely be slow and expensive.
Deeper Dive: Limestone to Cement (and back again)
In 2019, approximately 7% of global emissions came from the concrete used in buildings and roads. Common concrete used in buildings is made up of 60% to 75% of sand, gravel, and crushed rock (called aggregates), 7%-15% cement, the rest from water and air. Making cement is the source of most of these emissions.
Calcination
Most of those emissions come from roasting limestone (calcium-carbonate ) to form the active ingredient of cement, quicklime (calcium-oxide
). More than half of those emissions (58%) are chemically released from the limestone as it breaks down. The rest of the emissions come from the fossil fuel needed to supply the heat and the electricity needed to grind and process it into cement powder.
About 40% of the emissions are from burning fossil fuel for heat:
Carbon + Oxygen → Carbon-dioxide + Heat
About 60% from calcination:
Limestone + Heat → Quicklime + Carbon-dioxide
Even if all the energy could come from non-carbon sources (renewables, nuclear, etc.), the total emissions would still make up more than 4% of total global emissions.
But the story is more complicated than just the initial production of cement.
Carbonation
Once the concrete is mixed — it quickly becomes solid building material. However, the cement in the concrete is still chemically active – as both quicklime () and slaked lime (
). It starts reabsorbing
from the air, once again becoming limestone (
) through a process called carbonation.
Slaked Lime (Calcium-hydroxide) + Carbon-dioxide → Limestone + Water
or
Quicklime + Carbon-dioxide → Limestone
This process is very slow and depends on how easy it is for the to penetrate the concrete. This is an active area of research, but many studies suggest that even after half a century, only a relatively small portion of the cement has been converted back to limestone.
However, at the end of the concrete’s useful life it can be broken up and ground into a powder where it can much more rapidly absorb . Once the chemical process is complete, the
chemically released during its production will be reabsorbed. The
from burning fossil fuel will not.
1 Puettmann, Pierobon, Ganguly, Gu, Chen, Liang, Jones, Maples, and Wishnie. 2021?. Comparative LCAs of conventional and mass timber buildings in regions with potential for mass timber penetration. Sustainability special issue – Mass Timber and Sustainable Building Construction. In review.
2 ibid.
The Greening of the Grid
A Future Built of Wood
Previous
Next